アナログな織物産業の「生産管理」を熱意と対話で改革する、BtoBシステム開発への挑戦【地域課題解決型ハッカソン vol.3 エルトップ】
ITの力を使って、今の業務を効率化したい。そう思っても、これまで築き上げてきた仕事の流れを変えるのはそう簡単なことではなく、実現には数々の調整が必要だ。アナログな作業工程や業界慣習が多く残る伝統産業であれば、なおさらだろう。
富士吉田の織物産業も、おそらくそうした「DX(デジタルトランスフォーメーション)」が最も進みづらいジャンルの一つ。けれど、担い手の高齢化や人口減少などを前に、改革は間違いなく必要……そんな状況に風穴をあける取り組みが、「地域課題解決型ハッカソン」だ。
神奈川県横浜市のプログラミングスクール「ディープロ(DPro)」の受講生たちが、卒業課題として富士吉田市の機織企業の課題解決のためのシステム開発を行う。地域も業界も越えた本取り組みはこれまでに2回行われ、各回ごとに実績が生まれてきた。
その第3弾となる今回、お題となったのはいわゆるBtoB事業の「生産管理システム」。プロジェクトを最初から見てきたプロジェクト担当者も「今までで最も難しい課題」だと語った第3回は、最終的にはDXやプログラミングという観点だけでなく、BtoB事業におけるビジネスの勘所、協業を成功させるために最も大事な要素など、様々な観点から示唆に富んだ結果に。加えて、今回は一般IT企業・株式会社リンクレアで働く現役エンジニアたちからも参加希望の申し出があり、計2チームでのハッカソンとなった。2日間で見えてきた現状を変えるヒントを、「現状を変えたい」と願うすべての人に向けて、本記事ではできる限り詳細にお伝えしたい。
電話確認がベースの生産状況を「誰もが見てわかる」状態にしたい
IT・デジタル技術によって仕事をより良く変革していく「DX」。口でいうのは簡単だが、しかし実際には、どこの過程をどのようなサービスを入れて改善するのか、その後どのように運用していくのか。そもそもどこに問い合わせるのが正解か?……考えなくてはいけないことや不明瞭なことが多すぎて、「現在の業務フローを、IT化することでもっと効率化したい」という課題感は持ちながらも、時間やコスト、リソース問題から現実的に進められていない企業、現場責任者は少なくない。
今回、「地域課題解決型ハッカソン」の第3回目に参加した株式会社エルトップもそんな企業の一つ。ジャケットなどに使われる高級裏地素材を企画・生産・販売する同社は、アパレルメーカーなど衣服の企画・製造を行う企業を主な顧客とし、完全なBtoBビジネス一筋で、一流ブランドを主要得意先として抱える現状の地位を築いてきた。
今回、参加するIT人材たちが挑む課題は、この生産管理を解決すること。というのも、ベンベルグ(キュプラ)を使用した織物「LOISIR®」(ロアジール)をはじめとする商材は、取引先である全8社の機屋に製造を依頼しているのだが、その各機屋とのやり取りがすべて電話によるものなのだという。生産管理を一手に担う八木高志さんはこう話す。
八木さん:
「機屋さん……要は、一番最初に生産現場に材料が入って、どの期間でこの頼んだものが上がってくるかという対応スケジュールを、今まですべて電話のやり取りでやらせていただいてたんです。我々が今現状欲しているのは、そこにITを入れることで、そういった連絡をしなくても(生産状況の)情報が取得できるような仕組みです」
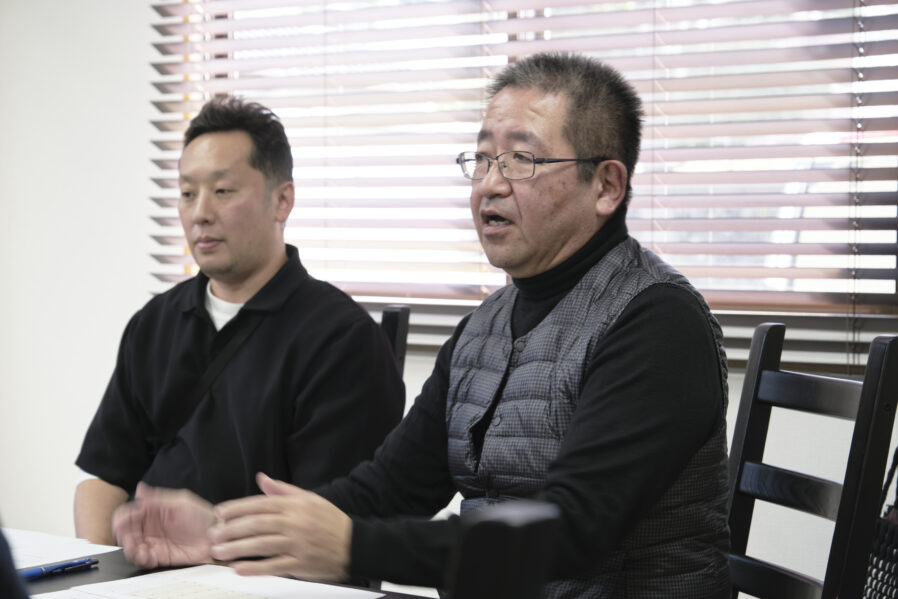
▲株式会社エルトップ・八木高志さん
エルトップの本社は東京にある。普段は東京にいる八木さんが、富士吉田に工場を構える機屋の各社と電話で、つまりマンツーマンでコミュニケーションをとって進行管理している。役目を担うのが八木さん一人のため、営業担当者など社内の誰かが「この取引先のこの商品の生産状況を確認したい」という場合も、八木さんに聞かないとわからない状況なのだという。
八木さん:
「社内にいる人間も、『この商品のこれがいつ上がってくるのか』と、情報を知りたいとなった時に、もう大体僕に聞かないとわからなかったりする。それが今後、タブレットなりパソコンの機械なりにそういう情報が入ってくれば、誰もが見て目でわかる。そうやって少し楽になれないかなと。そうすれば機屋さんも、機屋さん自身がそこに(生産状況の情報を)打ち込んであげておいてもらえれば、都度都度電話する煩わしさ、電話を受ける煩わしさも軽減されるのかなというところなんです」
課題に取り組むのはエンジニアの2チーム
きちんと課題を解決しうるシステムは、やはり現場を見ないことには作り上げられない。2024年11月、こうした課題感や実際の業務フロー、どんな仕組みを実現したいのか等、基本の要件をオンラインで八木さんとやり取りした上で、いよいよ富士吉田にての現場視察の場が組まれた。
今回、参加したディープロチームは2人。
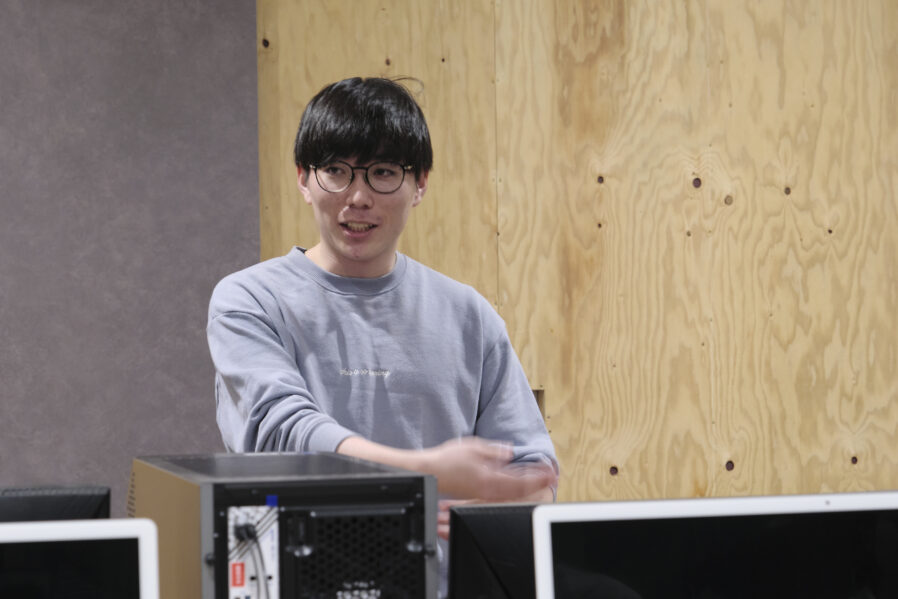
▲ディープロチーム、荻野さん
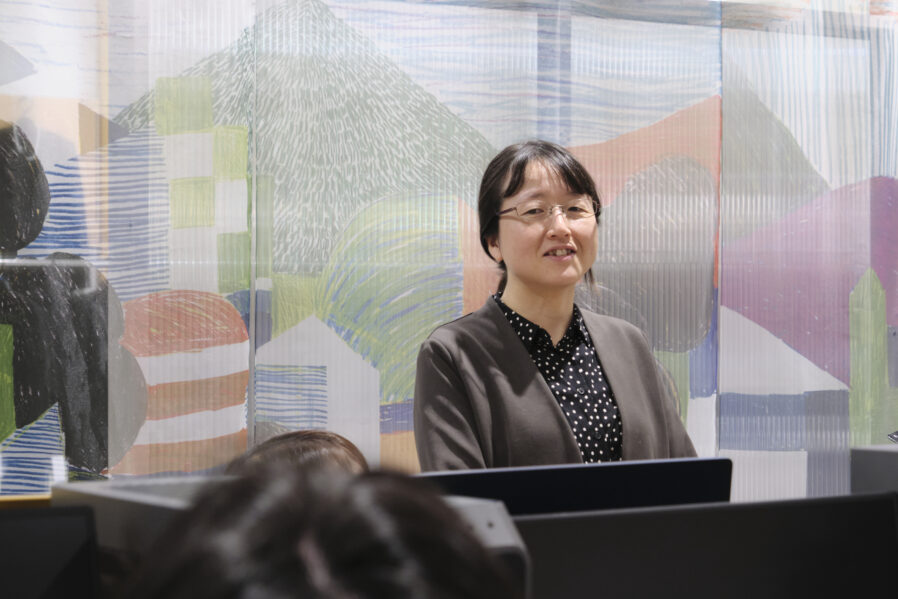
▲ディープロチーム、高野さん
ディープロチームとして、今回エルトップの課題に挑む荻野さんと高野さん。二人とも社会人として働く中で「自らつくって課題を解決できる」ようになりたいという思いからプログラミングスキル習得を考え、ディープロの門を叩いたという。
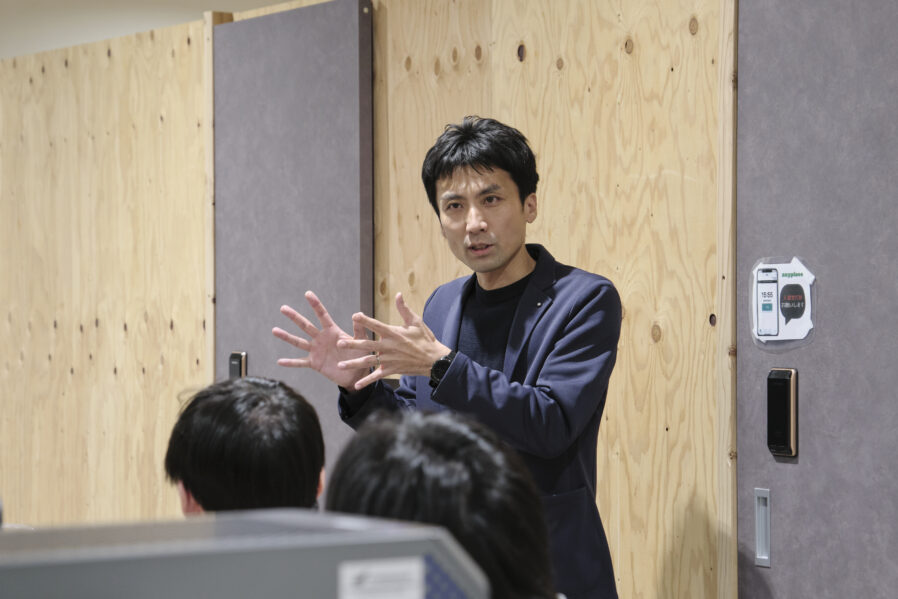
▲株式会社リンクレア・部田裕介さん
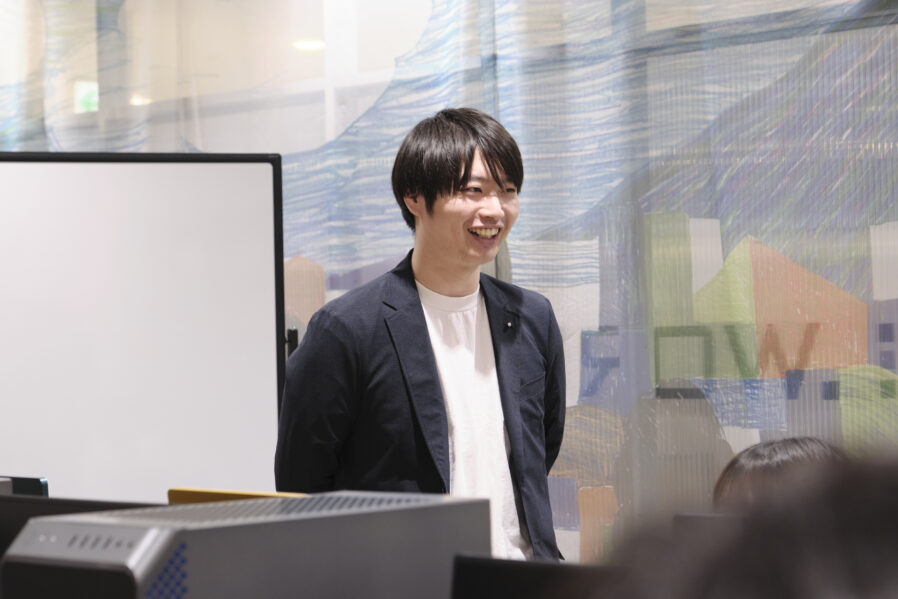
▲株式会社リンクレア・渡邊千貴さん
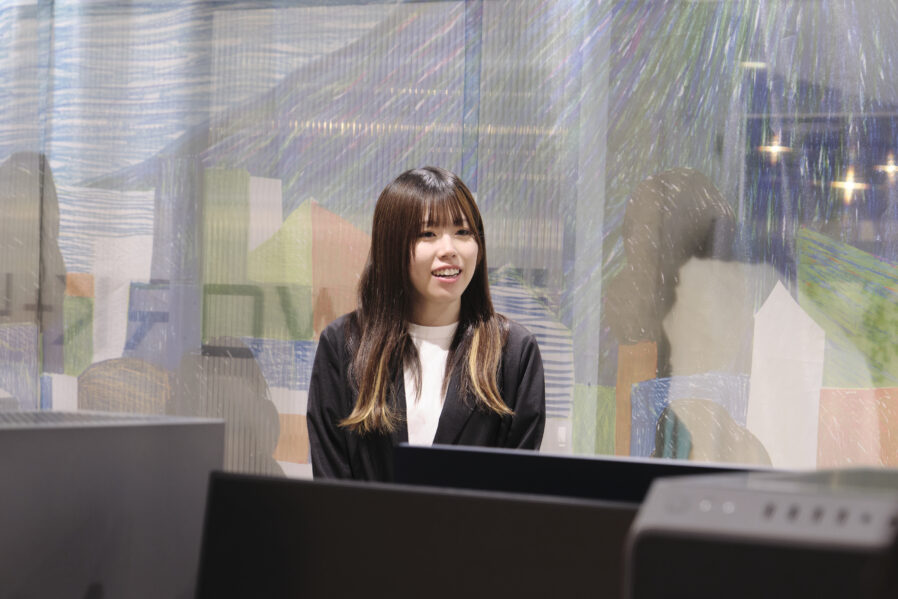
▲株式会社リンクレア・高田紗也秋さん
そして東京のIT企業である株式会社リンクレアからは、現役で開発現場に携わる3名が参加。リンクレアは、SIer(※1)と呼ばれる、顧客となる企業に対して一貫してシステム開発から提供、運用までを行うBtoBを専門とするIT企業だ。富士吉田出身の渡邊千貴さんが地元の事業に仕事として何か関わりたいと探っていたところ、前回までのハッカソンの取り組みをネットで発見。会社としてぜひ参加したいと手を挙げた。
※1 エスアイアー。顧客のITシステムのコンサルティング・設計・開発・運用を一貫して請け負う「システムインテグレーション(SI)」を行う事業者のこと。
布はどのようにできあがるのか?まずは生産工程の仕組みを理解する
前回と同じく、講師やメンターも含めたメンバー全員が自己紹介を行うところからスタート。エルトップからは八木さん、そして取引先となる機屋を代表して有限会社オサカベの代表・刑部正之さんが同席した。早速、生産現場の一つであるオサカベの工場へ。
今回の肝は、全体の生産フローを正しく捉えるところにある。取引先となる関係者が複数存在し、複雑に諸条件が絡まり合うBtoBビジネスの現場。そのシステム開発は、正確に各社の関係性や情報伝達方法、意思決定のプロセスなど諸条件を掴んでいかなければならない。想像力とコミュニケーション能力がものをいうというのは、前回までと同じだが……。
まず、参加者に渡されたのは、3枚の紙。エルトップ側のジャカード織機(しょっき)による生産予定表だという。……が、アルファベットと数字の組み合わせ、何かの工程ごとの日付が並んでいるということ以外は、それらが何を示しているのか素人目にはまったく見当もつかない。
八木さん:
「これはジャカード(織)の生産予定表です。我々が日々機屋さんとやり取りをしてる中で、機屋さんからいつ頃にこういうものが上がってきますよというのを、こういう表の形で出していただいてる予定表が存在します。ちょっと日付がアバウトな表にはなっているんですが、ここがもう少し機械というか、何か(デジタル技術を)入れ込んで、数字が見えるような資料とすることができないかなと」
確かに、日時は書き込まれてはいるが、文字ベースの資料なので、視認性は決してよくない。ぱっと見で、何がいつどのタイミングでどういう状況になるのか、つかみづらい状態だ。そして各社ごとに表のフォーマットもバラバラ。これでは、情報管理も煩雑になってしまう。
機屋の生産管理は難しい、ヒントは制作フローと関係図に
基本的にはエルトップの展開している商品は、同社が独自で定番商品として持ち合わせているもので、客先からの別注であることはほとんどない。依頼主である企業担当者は、エルトップの定番商品が並ぶ見本帳を見て品番を選ぶ形だ。在庫があればそのまま納品するし、在庫がなかったり、営業担当とアパレルメーカーとの商談で先々に量産に繋がる可能性があれば八木さんは各機屋に織ってもらい、完成品を収めてもらうことになる。
見本帳を見たアパレルメーカー等から発注がくる(エルトップの営業担当者が対応)→機屋に生産依頼(エルトップ生産管理の八木さんが対応)→機屋に織ってもらった完成品を納品(富士吉田のエルトップ配送倉庫にて保管ののち出荷) ……という流れだ。
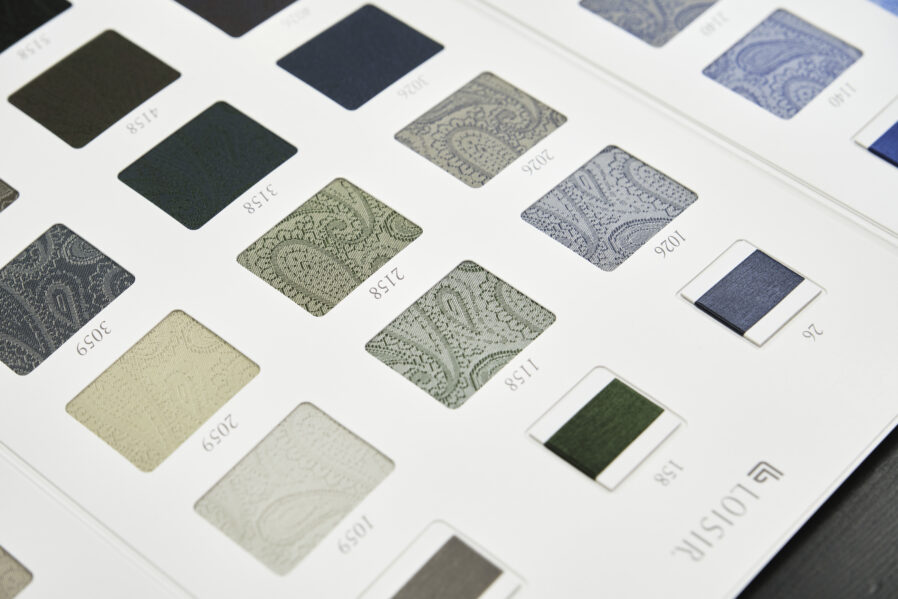
▲エルトップの主力製品「LOISIR®」(ロアジール)の見本帳
定番品として型が決まっているのであれば、エルトップ側で各社共通の一つのフォーマットを決めて運用すればいい気もするが……ことはそう簡単ではない。これが今回の肝、本題の部分である。八木さんは、紙の一枚を見ながら、その読み解き方を解説した。
八木さん:
「この生産予定表で説明すると、ここに書かれている『1号織機はこの連続で織っていってくださいね』というのは、僕と機屋さんとのやり取りで決めています。他の織機に回してもできなくはないですけど、機屋さんとのやり取りの中で順番よく織れる流れを決めています」
織物は、基本的に経糸(たていと)と緯糸(よこいと)の組み合わせになる。複雑になるため詳細な説明はここでは省くが、織機に対する経糸の準備には膨大な手間が必要なため、あらかじめ各機屋の織機ごとに経糸が決められている。つまり、織機ごとに「織れるもの」が決まっているのだ(黒の経糸で織りたいなら織機A、赤なら織機B、という具合に)。
なので、アパレルメーカーなど依頼主の注文を元に「この品番のこの規格(糸と柄の組み合わせ)ならこの織機だから、オサカベさんに発注」というように、発注先の機屋が決まる。だが、実際に「その機屋のどの織機でどのタイミングで織るか」は、エルトップ側で決められるものではなく、各機屋の判断に委ねられる。機屋各社はエルトップの商品以外にも複数社の商品の生産を担っており、それも踏まえて稼働スケジュールを管理しているからだ。この点が、生産管理を複雑かつ難しくしている。
依頼してから仕上がるまでは、その機屋のその時の生産状況にも左右されるし、各社それぞれ生産体制や所持する織機の状況も異なるから、厳密には生産管理担当の八木さんとしても、「管理」しきれるものではない。前述の各機屋からの生産予定表が形式もバラバラなのは、機織産業がこうした各工程を担う事業者の独立性の元で成り立ってきたことも関係しているのかもしれない。
こうした業界慣習も絡んだ細かな事情や背景を、八木さんの説明に対して質問を投げかけていくことで少しずつ紐解いていく。今回の課題で解決すべき本質的部分を確認しながら。
八木さん:
「僕ら(エルトップ側)は、こういう紙や電話での聞き取りになっている『機屋さんの現場にもの(糸など)が入って、いつどういうタイミングで出てくるのか』という情報が、他の誰が見てもわかるような、何かそういうシステム的なものができれば、非常に楽になる。機屋さんも電話で(上がりは)いついつです、っていうようなやり取りをするよりも『これを見てください』って言った方が早いと思うし、そういう会話もおそらく(今後は)なくなってくるのではないか。(生産工程での)肝心なところの話は(電話でのやりとりが)必要かもしれませんけど、商品の上がりの予定日に関しては電話で四六時中やり取りをするものでもない。できればそれを目で見える何かにしておいた方がいいのかなと思ってます」
発注書の各予定日が「アバウト」になる複雑な理由とは
また、もう一つ難しいのは、どうしても納品日や一つの工程が終わる予定日程がアバウトにならざるを得ないところだ。これは、一枚の織物が織機で織られるまでに、数々の工程を踏む必要があり、そのそれぞれに専門業者がいて分業されていることによる。例えば、糸に関してもそうだ。糸を作るだけでなく、染めたり、「糸を織機にセットする」=整経(せいけい ※2)という工程がある。
八木さん:
「糸は染色屋さんで染めていただいて、今度は整経屋さんでこのストライプのラインを組んでいただかないといけない。糸を1本ずつこう引っ張ってきて、それを全部こういうストライプ状に並べて、それが初めてこういう風に織物になる」
※2 富士吉田における「整経」についてはこちらから詳しく知ることができる
https://hatajirushi.jp/all/ordertextile/seikei
エルトップから発注を受ける機屋側の立場としては、どう考えるのか? 質問を受けて、刑部さんは工程についての補足をしてくれた。
刑部さん:
「この産地は分業の産地になるので、機屋さんはもう『織ることのみ』なんですね。織りもある程度生地を(一度)織り出せば、ある程度の納期は見れるんですけど、その前の工程となると、自社じゃない。商品(糸)が入った順で、という形になるので。そういう関係でかなりアバウトであると。その後の工程、織り上がりの後の工程も、『整理加工』(※3)と書いてあるところは他社さんになるんです」
※3 富士吉田における「整理加工」についてはこちらから詳しく知ることができる
https://hatajirushi.jp/all/ordertextile/seiriato
この各種別工程についても、人手不足や高齢化などで発注可能なタイミングが限られているなどの事情があり、その前工程のスケジュールが少しズレただけで、後の工程との兼ね合いで織上がりのタイミングが大きく後ろ倒しになることもある。さらに影響が大きいのは、一番最初の糸の部分だという。エルトップを始め、富士吉田の機屋が危惧しているのは原料となる糸の納品タイミングだ。富士吉田の機織産業を支える一つの要因となっているのは、旭化成による「ベンベルグ®」(キュプラ)を扱えることであるが、富士吉田以外での需要も高まり、糸の供給タイミングが非常に不安定で読みづらいという。
八木さん:
「あと、産地の中でも、たとえ原糸が入ってきてもその後に、染色(糸を任意の色に染める)までの間に『撚糸』(※5)っていう工程があるんです。そこが、撚糸屋さんの数が後継者不足でこの富士吉田の産地、激減しておりまして、撚糸キャパ(が不足している)っていうのも1つ(の要因としてある)」
※5 富士吉田における「撚糸」についてはこちらから詳しく知ることができる
https://hatajirushi.jp/all/knowfactory/3043
リズミカルに布を織る織機を前に、聞いた情報と実像を擦り合わせる
すでに初めてのワードのオンパレードで頭がいっぱいではあるが、前提要素となるヒアリングがある程度できたところで、いよいよ織機が並ぶ工場を見させてもらうことに。
写真では伝わらないが、工場内は織機が稼働しているためかなり賑やかだ。会話するには相当相手の近くに寄らないと聞き取ることも難しいほど。刑部さんが、経糸と緯糸、ジャカード織機とドビー織機の違い、各工程を担う機械など、説明してくれるのを聞きながら、実際の織機を見て「経糸と緯糸とはそういうことか!」など、事前ヒアリングを腹落ちさせていく。
どんなシステムで解決するのか?目指すのは受発注両者に便利なもの
こうしたヒアリングから見えてきたのは、布ができあがるまでには多くの工程が含まれており、ステークホルダーが多数いること。そして、多くの要素が絡み合うために、コントロールや予測できない点が多いということだ。
一度工場で実際の機械を目にして、布が織られていく過程を大まかに頭でつかんだ後に、もう一度ヒアリングの時間があった。細かな質問が重ねられ、開発するシステムの仕様を左右する要素を各々が丁寧に拾い集めていく。
参加者:
「エルトップさんとオサカベさんのお二方に質問なんですが、人手って不足しているんでしょうか? 仮にシステム化した場合、余った時間を何に使いたいという展望はありますか?」
刑部さん:
「自社の工場は人手は不足してないですね。フル生産した場合は、不足かちょうどいいぐらいなんで、とりあえず今の(雇用)状態をキープしないとっていうのはあります」
八木さん:
「うちの場合は、富士吉田にある配送倉庫には今、常時4名がいるんですね。それがちょうどベストな人数でもあるんです。一方で、今僕が東京でやってるこの産地の生産管理の仕事を、今後誰に引き継ぐのか。……なかなかその次の世代に渡すっていうところまで行ききれてないんです。もう少しIT化を進めて機械で物が見れることで、他の人間、特に営業が僕に必ず聞かないと(商品の状態が)わからないっていうところが少しでも軽減できればなと。 彼らが見て、客先に(商品の生産状況を)答えられる何か手がかり、取っかかりとしてそうしたシステムを活用させていただければいいなと思います」
今回のシステム導入主体となるエルトップと、その取引先となる機屋。システムは両者が使うことになるため、どちらにとっても使いやすいものでなければならない。重ねてのヒアリングができたところで、お次は八木さんのお話に出てきたエルトップの配送倉庫に向かうことに。
エルトップの配送倉庫へ。在庫管理と出荷フローはどうなっている?
車で移動し、エルトップの配送倉庫(生産物流センター)に到着。ここで在庫をどのように管理しているのか、どのように出荷依頼がきてどのように対応しているかを見ていく。
案内してくれたのは、生産物流センター 所長を務める吉澤直亮さん。東京の本社(事務所)から出荷指図書という資料が入ってきて、それに基づいて出荷をしているという。
吉澤さん:
「『ラインプロ』という販売管理システムを使って、入ったものは入荷処理して、出てったものは出荷処理して管理してますね」
エルトップで現状導入しているいわゆる基幹システムに当たるものは、この販売管理システムのみ。八木さんいわく、すでに20数年ほど使っているもので、機能としては商品の入荷と出荷の数を記録するのみだという。一部はパソコン上のデジタルデータでの記録ができるものの、出荷に関するやり取りもこの機械で完結するわけではなく、手書きとFAXを組み合わせて使う必要がある。
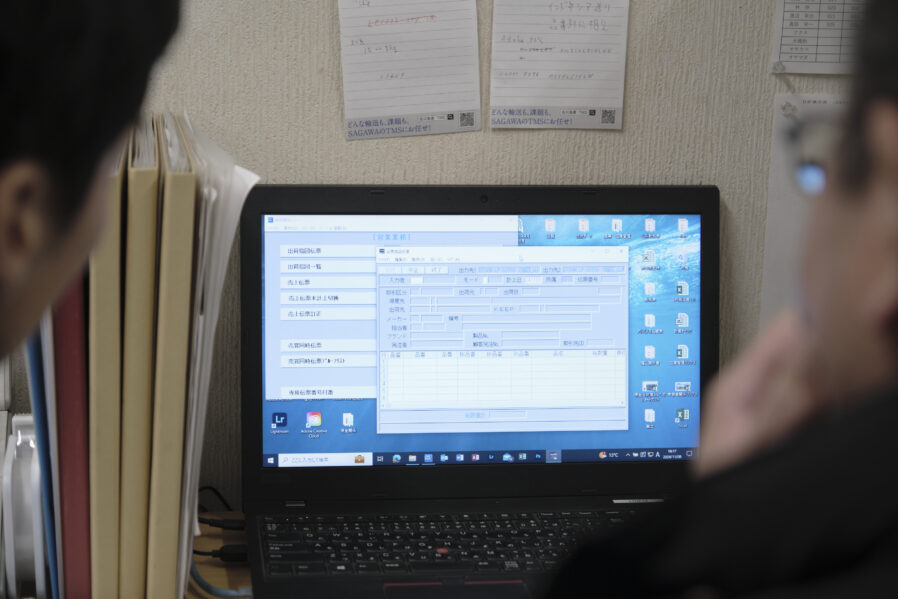
▲受発注の情報や在庫情報は全部このシステムに入っている。会社の運営を背負う、非常に重要な存在である
八木さん:
「一応システムでプリントアウトされるんですが、ただ、(在庫が)なしだという情報に関しては、こちらから手書きで出してFAXをしている。そこに対して、いつ生産が組まれて『いつ頃入荷する』というやり取りも、そこもFAXですね」
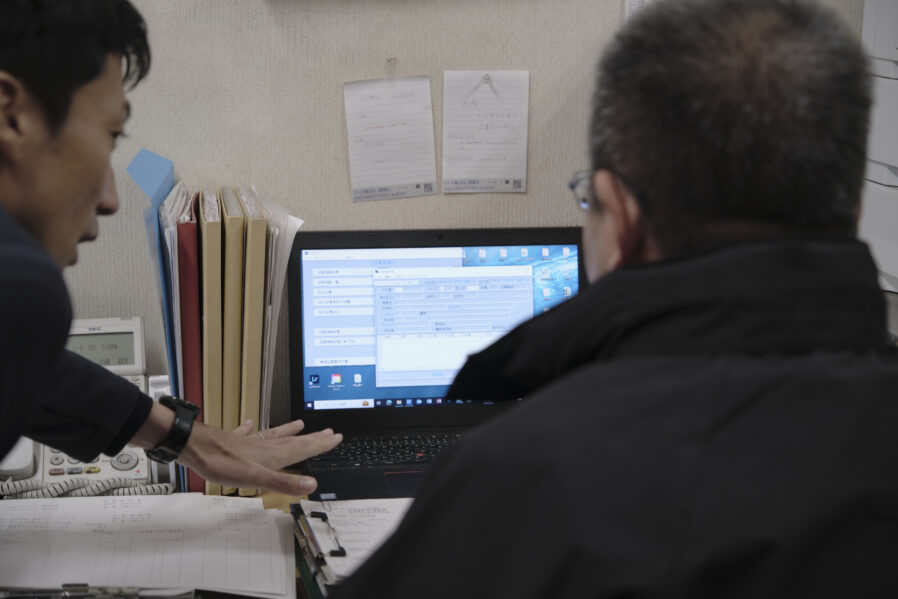
▲机の上に乗っている出荷指図書を見せてもらうと、手書きされた跡があった。在庫があればシステムでやり取りできるが、在庫がない時はFAXで諸々やり取りをしなくてはならない
地域産業における商社機能を担うエルトップにとって、在庫管理は何よりも重要。在庫があまりにも残っているのは問題だが、一方で「在庫がないのでこれから生産します、納品できるのは半年後です」というのでは受注先を逃してしまいかねない。在庫数のコントロールが、事業を支える根幹となる。
八木さん:
「特に今の吉田産地の先染めの織物に関しては、 我々がこういうサンプル帳の販売をしてるんで、売れなくてもある程度は在庫を持っていないといけないという面もあります。商売としては、必要な時に必要な量を持つのが当たり前のことだと思うんですけど、多少(在庫を)抱えてないといつ注文が入ってくるかわからないから……特に営業は客先に対して『品切れです』っていう言葉が一番言いたくないものですから。いつでも来てください、ありますよっていう風に言いたい。そうすると、どうしても自ずと在庫が過多になってしまうケースも多い」
在庫管理の要となる棚卸しも、アナログ作業で
在庫管理という観点だと「棚卸し」の作業が要となるが、通常どうしているのか? 聞くとこれも半分手作業によるものだという。在庫となる布は、筒状に丸められて棚におさまっている。その筒ごとに紙のカードが差し込まれているのだが、これがそれぞれの商品(布)の品番となっており、これをチェックし在庫数として数えていくのだという。
八木さん:
「棚卸しが手作業みたいなものなんですよね。年に2回、8月と2月の月末にここ(富士吉田の生産物流センター)へ来て、営業はこの棚を見て、カードの数字を読んで書いて、また本社に持ち帰って集計作業をする。基幹システムに入力してはいるんですけど、その数字が時々番号の見間違えだったり、差が出るケースがごく稀にあったりはしているんです」
また、営業がキープしておきたい商品があった場合、基幹システムにそのキープ数を入力できる項目が設けられてないため、その分はExcelで別で管理している。そのため、基幹システム上では在庫数が十分あるように思っても、その別途管理しているExcelファイルで営業キープ数を確認し、それを差し引いた数が「いますぐに販売が可能な数」となる。これだと客先から「この品番をこれくらいの数欲しい」という問い合わせへ答えるだけでも、手間がかかってしまう。
誰の何の問題をどう解決するのか。課題の本質を見極める
工場から帰ってきた参加者たち。いざ作業に入る前に、野呂さんから進め方についての重要な考え方についてのレクチャーを受ける。そこで念をおすように伝えられたのが、プロダクト開発において最も重要であると言える、「何をどうつくるか」設計を組み立てる上での考え方だ。
野呂さん:
「今日ヒアリングさせていただいて今、皆さんの脳みそは『今持ってる問題はどうやって解決すればいいのか』ということで一杯かと思います。問題解決したい、問題解決したい。……そうなると何が起こるか。『誰が何に困っているのか』を忘れるんですね。聞いた内容に対して具体的な個別のことばっかりを考えると、例えば在庫管理システムはこんな仕様だったらいいかな、こんな画面だったらいいかな、ここで使えたらいいんじゃないかなとか、そこばっかり考えちゃうんです。本当に困ってることから遠ざかってしまう。そういうことが起こってしまうので、まずは『誰の何の問題をどう解決するのか』……この順番で、考えてみていただきたいと思います」
ここで考えるプロセスの参考として紹介されたのが、「スタートアップ・フィット・ジャーニー」(※6)というフレームワークだ。何もない状態から課題を定義し、そこに対する必要なサービスを考案して、新しく会社を創業したりベンチャーキャピタルからの投資を得るスタートアップ企業の起業プロセスでよく使われる枠組みだという。これに則って、まず誰が何に困ってるのかという観点から整理して設計を固めていくと、本質的な課題解決のための策を導きやすくなるというわけだ。
※6 「スタートアップ・フィット・ジャーニー 今どの段階にいて、何に取り組むべきかのガイド」(東京大学『FoundX Review』)
https://review.foundx.jp/entry/startup-fit-journey
どんな製品や解決策を提示するかよりも、まずは課題を正しく選定しなくてはならない。その日、それまでに見聞きしてきた中にも、課題らしきものはいくつもあった。どこにフォーカスするかを決める必要がある。
野呂さん:
「今日もいくつも観点がありましたよね。エルトップさんの立場で困っていること、機屋さんが困っていること、糸を作ってる方が困ってることなど。立場によって困ってる内容も違えば、そのレベル感も違えば、様々ですよね。必ず誰か1人に絞らなきゃいけないってことはないです。何か一つの問題、課題っていうのが実は他にも繋がってるってことはあります。なので、どんな仕様にするかといった話からではなくて、誰の何の問題を解決するんだっけ、というところからまずチーム皆さんの認識を合わせて、そこから一緒に議論してもらうとスムーズになると思います」
誰が何に困っているのかを整理できたら、次に『その課題は何かしらの解決策で解決できるのか、あるいはできないのか』を考える。
野呂さん:
「これを『プロブレムソリューションフィット』と呼びます。(困っていることとの中には)解決できないこともあるかもしれないですよね。今日は、糸の製造については正直我々のシステムでどうにかなる話ではないという判断を、皆さんされたんじゃないかなと思うんです。そうやって考えた時に解決できないエピソードだったりすると、考えてもあまり意味がないということになってしまう。なので、『何であれば解決できるのか』ということを考える。つまり、解決策はあるのかということですね。その上で、じゃあその解決策って、製品として実現できるんだっけ?というのを、ようやくその後に考えていくんですね。この順番で考えていくのが大事です」
限られた時間の中で、依頼主の抱える解決したい課題を、最適と思われる方法で、プログラミングという手法で解決してみせる。これが、エンジニアに求められる技能の核の部分だとすれば、課題を選定し間違えれば、時間も労力もロスになり、案件失注も起こりうる。
エンジニアとしてすぐに現場で活躍できる人材を育てることを目指すディープロでは、プログラミングスクールのカリキュラムの中に、「カタログ設計」という考え方を取り入れているという。簡単にいうと、顧客、つまりカスタマーのメリットを起点として諸要素を整理し、具体的な機能など仕様の設計を進めていく方法。エンジニアが「作りたいものを作っちゃう」ことを避けるために、顧客から見た時のメリットをまず書き出してみるというフォーマットだ。
野呂さん:
「使われないものを作ってしまうのではなくて、顧客が喜ぶことを目指して一緒になって作ること。まさにエンジニア、作り手こそこういう発想でいてほしいと思います」
続けて野呂さんは、今回現場で得られた情報を生成AIに投げ込んでみたところ挙がった提案を例として見せた。「正解」ではありそうだけれども、どれも抽象的で具体性に欠けるものが並ぶ。「こうやって、AIにそのまま作らせると抽象的になってしまう。人間が考えて、その方の肌触り感とか、実際の現場を見た時のその方の感情とかを配慮したりすると、もっと具体的でピンポイントに解決できるものを見つけられるんじゃないかなと思っています」
今回は、ディープロチーム・リンクレアチームと2つに分かれて発表することとなる。早速、野呂さんの講義の後にそれぞれのチームに分かれて課題整理と発表のための準備に入った。どのように課題を定義し、そこにどんなソリューションを設計するのか。あらかじめオンラインで行ってきたすり合わせ内容に重ねて、今回見聞きしたもので得られた気づきを元に、組み立てていく。
2日目、いよいよ発表へ。2チームが出した結論は?
迎えた2日目。午前中は昨日の続きの作業時間を行い、発表時刻までブラッシュアップを行う。各チーム、プレゼン時のシナリオ確認、それに合わせたスライドのつくりこみ、トーク練習などチームそれぞれ連携プレーを発揮しながら取り組んでいく。最後の追い込み、どこまでできるか。少しピリっとするくらいの集中力がその場に満ちた。
そしてタイムアップ! 各チームに与えられた発表時間は10分。先行としてディープロチームからプレゼンを行う。
ディープロチームの提案:「織機のモニタリング機能」で一目瞭然に
まずはあらかじめ提示されていた課題点をおさらいしながら、現在の業務フローにおいて、電話応対をベースとしたやり取りで属人化が起こり、発注管理が煩雑になっていると説明。紙や手、場合によっては人の記憶によるアナログな情報管理によってしまっていることで、エルトップ、機屋それぞれ現在の在庫状況や履歴、生産状況に関する情報管理ができていないことが課題となっていると指摘し……
それを解決するものとして、「織機のモニタリング機能」の実装を提案した。エルトップと各機屋の二社間で現状が可視化できることで、双方の煩わしさを軽減しよう、という考えだ。
双方で情報共有することで、織機ごとの稼働状況を可視化。「現在どの工程で進行しているのか」を確認できるようにした。各工程ごとに予定していたスケジュールから遅れると、アラートが出る仕組みだ。確認のために電話連絡する手間もない。
また、「誰もが見て目でわかるもの」という八木さんの意向を汲んで、テキストベースだったスケジュール情報をガントチャートのデザインに。工程ごとに色分けし、視覚的に瞬時に捉えられるようにした。
とてもわかりやすくなって、良さそうだ!
……と、そこで野呂さんから鋭い指摘が入る。
「機屋さんにはどんな内容をいつどう入力してもらうっていうような考えでいらっしゃるんでしょうか?」
その情報があることが大前提であるが、機屋さん側はどのように情報をそのシステムに入力する想定なのか? それに対して、ディープロチームは「エルトップ側から織機に乗った時点で入力する想定」と回答。
「できれば方針としては、機屋さんの入力が少ない方がいいので、事前にこちらで把握して織機を登録してあるというのが良いと思いました」
さて、エルトップ側としてはどのように映ったのだろう?
八木さん:
「本来であれば機屋さんの方で主体的に入力して、僕らはその情報を吸い上げるみたいな形の方が良いのかなと。織機に関しては固定で、この品番のこの色は必ずこの織機に、というのは、僕らの方であんまり指図ができない部分もあったりするので、そこに関しては、機屋さんがもうちょっとやりやすいような形でできる方法が一番ベスト。その時々の状況によって、僕らが想定してた、例えば織機Aにのせてほしかったのが今回ちょっとトラブってるからBにのせるよとか、その辺の判断も機屋さんの方じゃないとわからない部分もあったりするんで」
実際に織機に乗せるタイミングや織機の選定は、機屋さんでないとわからない。エルトップ側で入力した場合、確認のための電話のやり取りが結局発生してしまうので、できれば機屋さん主体で情報は入力いただくのが良い……ということだった。
また、生産管理担当である自分としては、非常に見やすくて良い、と前置きしながら、すべてが可視化されていることへの懸念点も述べられた。
八木さん:
「僕はこういう日にちが追っかけで分かる方がすごくありがたいなと思いますけど、もう少し(お互いの情報が)隠れててもいいのかなというように思います。 機屋さんからすると、もうこの日にちに必ずあげなきゃいけないのかっていうプレッシャーみたいな部分もかかっちゃう時もあるんで、そこが一概にいいのかなというのはちょっと思いました」
実際には「発注主側が発注したら即時生産に入れ」とはいかない。発注者と受注者がそれぞれ独立している対等な関係であるからこそ、すべてを明らかにすることが必ずしも解決とはならない……システムが、企業間の関係性やパラーバランスにも影響を与えうる。あくまでも「人」が使うのだということを改めて認識させ、BtoBビジネスの開発の怖さを垣間見た気がした。
リンクレアチームの提案:FAXとも共存したストレス最小限の管理システム
続くは、リンクレアチームの発表。こちらも、まずは現状課題から確認。
その後で、現状の業務フローを図式化して整理。今が具体的にどんな状態で、それがどのように変化する形を提案するのか、わかりやすく提示した。
システムで発注書を作れるようにしながらも、従来のFAXでの機屋への発注という形はそのまま崩さずにあえて残した。その後、機屋側で、開始予定・終了予定・完了報告などの進捗情報をシステムに入力。そうすると、自動でエルトップ管理者側画面に連携されて、エルトップ担当者は各社の生産状況が自社側の画面で確認できる……という仕組みだ。
オンラインで聞いていた課題を元に、事前に作っていたモックアップも披露された。進捗状況はなるべく入力に対する負担を減らすために、「30%・60%・90%」という大まかな入力形式にしたという。
FAXを残すなど、すべてを完全にIT化することを是としない点や、機屋さんに「この日までに仕上げろ」と強制力を感じさせたりストレスをかけないように配慮されているワード選び・デザイン設計が印象的だった。
エルトップ八木さんも、「非常にわかりやすいし、目で見てよくわかるっていうのがまず必要な部分なのかなと思うので、これは『開始・終了』っていうボタン1つでことが済むっていうことは非常にいいなと思います」と好感触なコメントが。
プラスアルファとして、さらなる拡張機能の提案もあった。今まで電話でヒアリングしていたものをそのまま自動で認識する音声入力にする音声入力機能だ。
「音声を文字列化して、それを入力項目に当てるっていう機能も実現可能です。現在の運用と変更点をなるべく少なくしようというところでできたらいいなと考えておりますが、まずはミニマムコストでやっていけたらなと思っています」
対話を重ねて、より良いシステムと未来をつくっていく
発表と質問の場を終えて、野呂さんは「こうしたプロセスを通して、より良い案を一緒に作っていく」のだと、まとめた。
野呂さん:
「質問やフィードバックを受けて、『あ、それ考えなきゃいけない』と思う部分もあったかと思います。プロだから一発で100点満点というのもおかしな話だと私は思います。コミュニケーションして認識が合わないところをすり合わせるプロセスがあるからこそ、質の高いものができると思っています」
最後のフィードバックタイム。エルトップ八木さんは、2チームの提案をどう受け止めたのだろうか。
八木さん:
「こういう生産管理システムのような、統一できる何かとっかかりみたいなものが必要だなって本当にもうずっと思ってまして。今回これをキャップクラウドさん(=本プロジェクト運営)にお話をいただいて、自分の社内で活用できるものが何かできればなと思って、参加させていただきました。短い期間でここまでできるんだなっていうのは思いました。すごく見やすく、デモを含めて、さすがプロだなと。なかなかこうしたプレゼンを受けたことがなかったので圧倒されたというところがありました。……今後においては、織機主体で一つ考えていただいて、システムを制作していただければと思います。僕らの方でもまた情報、情報の提供とかも含めてお伝えできればと思います」
ディープロチームとしては、まだこれから最終卒業発表まで、さらにブラッシュアップを進めることとなる。今回の2チームの案はこれから先、エルトップとしてDXを進める検討材料の一つとなる。今後に期待したい。
2日を終え、参加者たちからもそれぞれこの貴重な機会に対するコメントがあった。
リンクレア・部田さん:
「SIerの現場は、基本的にはもうオフィスでPCをカタカタ叩いて、0か1かの世界で……こういう他業種の方と会う機会が本当にないんです。あったとしても、同じSIerみたいな 。なので、実際現場で今回ご一緒させていただいて圧倒されるわけです。『ええ、あんなに音がすごいんだ』とか、そういう五感で感じることが、やっぱりアイデア出したりする上で、実際現場にいくこともすごい大切なことだと、今回我々は勉強させていただいたかなと思っております。今回我々も、会社としてもチャレンジでやってます。このご縁を大切にしていきたいと思うので、ぜひ引き続きよろしくお願いいたします」
ディープロ・高野さん:
「今回、初めてのチーム開発を実務でさせていただいたので、やっぱり認識を合わせるのが難しかったです。二人で(それぞれ)思っているのが違ったりするので、そのまま動いてしまうと、あとで『合ってない』となってしまったり」
ディープロ・荻野さん:
「役割分担も含めて、ちゃんと(相手の考えと自分の考えていることとを)擦り合わせるのが難しいなとは、やっていて思いました。一方で、個人だと逆に偏ってしまうところもある。どれだけ考えてもやりたいことが突っ走るということがどうしても出てきてしまうんで、そこはやっぱり個人でやるとなると難しい。特にクライアントワークとかだと……クライアントワークに限らず、BtoC(向けのプロダクト開発)のサービスを提供するにしても、使ってもらう人がどう思うか。自分の思想ではなくて、ちゃんと相手のこと考えて作れているかどうか。そこを考えないと難しいかなと思います」
エンジニアとして歩みを始めたばかりのディープロチームにとって、チームでものをつくる、という実践の場としても、今回のハッカソンで得られることは多かったようだ。
冒頭にも触れたとおり、3回目としてこれまでで一番難題な開発課題となった今回。それでも短い時間の中で具体的な形に仕上げていく姿は、開発を担う当事者でなくてもドラマを感じさせる力があった。この場が、また一人ひとり、それぞれの会社やチームにとって、新たなステージに進む一歩となるのかもしれない。
なぜ、プログラミングを学ぼうと思ったのか?と質問した答えの一つに、こんな返答があった。
「もうちょっとこうできたらいいのになっていう、自分でもし解決するならどういう方向でやるんだろうっていう気持ちがあって。まず自分がちゃんと作れる人になろうと思った」
思いやり、想像力。そして実行力。「誰かの課題をプログラミングという手段で解決する」エンジニアとして、一番必要なもの。その場にあるお困りごとを解決したい、目の前のその人のために。その思いと前向きな向上心さえあれば、いかにその山が険しくともきっと乗り越えて、まだ見ぬ景色に辿り着けるに違いない。
****
🌾今回の取り組みは、山梨県富士吉田市の主催する富士吉田市まるごとサテライトオフィスIT人材育成事業(委託先:キャップクラウド株式会社)の一環です。プログラミングスクール「ディープロ」を運営する株式会社ダイビックから相談を受け、2023年11月より富士吉田市にてスタートしました。今後も、DX化を目指す富士吉田市の各機屋と「ディープロ」受講生を結び、協業による地域課題の解決、地域産業の繁栄を目指します。
▼「富士吉田市まるごとサテライトオフィス」(略称:まるサテ)に関する詳細はこちら
https://prtimes.jp/main/html/rd/p/000000004.000093585.html
取材・写真・執筆/吉澤志保